An open source & global solution to the ventilator shortage:
The novel coronavirus (SARS-CoV-2) swept around the globe, infecting millions of people in nearly every country in the world. The disease it causes, COVID-19, has a range of impacts on its victims, with the most serious cases suffering from severe pneumonia and lung damage.
These most severe cases require clinical intervention to keep patients alive, with a primary means initially being the use of continuous positive airway pressure (CPAP) machines and ultimately invasive ventilation to ensure the patient receives enough oxygen and is able to breathe despite associated oedema. Although it is only a small percentage of patients that require these extreme measures, the rapid rate of transmission of the virus has created situations whereby ICU and ventilator capacities that would normally be adequate for a given population size are overwhelmed and patients cannot get access to this life-saving therapy.
Because modern ventilators are complex, highly-regulated and expensive devices, their manufacture cannot be quickly scaled to meet this demand in time to be effective, especially if the production is centralised and controlled by several key market players who compete using incremental technological improvements. This creates problems of accessibility of available products. Equally problematic is that the component parts of these systems are themselves in short supply as the entire medical supply chain has been stretched by the epidemic. There are also the intellectual property, distributorship, repair and other legal impediments to scaling the manufacture of ventilators or their component parts.
The community response has been for students, tech companies, and others to develop ‘ad-hoc’ ventilators to try and bridge the gap. In addition, to help solve the problem, special regulatory provisions were introduced to ease the minimal standards for “pandemic ventilators”. To date, none have been widely adopted for several reasons. First, many use ambu-bags and other equipment sourced from the same stretched medical supply chain and thus are unable to get parts. Second, clinical data have shown that patients with severe COVID-19 pneumonia have very fragile lungs, and improper ventilation can cause significant additional damage, actually worsening the outcome for the patient than if they had not received ventilation at all. Most of the ad-hoc ventilators proposed to date lack the fine control, measurement and feedback systems required to ensure they are not injurious to patients and have thus not been adopted by the medical community.
About PolyVent :
PolyVent is a diverse volunteer team of international engineers, scientists, clinicians and other professionals who have joined forces to design, build and produce a clinical-grade, open-source ventilator in response to the COVID-19 crisis and the resulting global shortage of ventilators.
Our approach is one of flexibility, with a modular design that allows modification of parts or whole modules to accommodate local supply chains and parts availabilities. Our system software can be calibrated to account for changes in key system parameters, allowing each ventilator to function as designed, even if the component parts are different from the reference specification.
Working with clinicians, we have also focused on ensuring PolyVent meets the complex clinical needs of COVID-19 patients, as well as having the flexibility to be used for treating other conditions, such that we maximize it’s efficacy now, and also leave a lasting legacy of equipment that can be used beyond the pandemic. As part of our design process, we have undertaken rigorous design reviews to ensure patient safety at every step, engineering failsafe protective features in each module. We are also planning to create VentCloud, a cloud-based data aggregation tool that will collect and analyse performance data from each PolyVent ventilator to identify failure modes, performance enhancements, and with clinician support, patient outcomes.
We realized early on that designing a ventilator, while a significant task in itself, is only half the battle. It needs to be able to be produced in the countries in which it will be used, both for logistical reasons, as well as to generate local economic benefits and create national pride. It also needs to be accepted by the medical community to be used and needs to be produced to proper quality standards, by organizations looking to help rather than a profiteer. Accordingly, we have designed an organizational structure built around country Clusters, which will have a leader in each target country, as well as supply chain, clinical, manufacturing and other personnel as needed. In this way we create a presence in each country PolyVent is deployed to, taking advantage of local knowledge and networks.
Current challenges that inspired us:
- The global shortage of ventilators due to the COVID-19 pandemic is causing preventable loss of life.
- Limited ventilator supply as the existing clinical ventilators are too complicated to manufacture, and improvised ones do not conform to the minimal clinical standards.
- Most of the ad-hoc ventilator designs do not meet the minimum standards or are non-scalable.
- We need alt-routes for acquiring ventilator components as the medical device manufacturers and supply chains are strained and broken at many places.
- We are facing an unprecedented crisis of our lifetime. We need to revise our production strategy to solve logistical imbalance.
- Lack of timely delivery due to entrenched bureaucracy, IP and distributor/repair issues.
- Difficulties in global R&D aggregation and adoption into production.
PolyVent operates like a bridging initiative between multiple semi-autonomous geographical clusters, centred around one adaptable design blueprint. The idea is to allow the creation of locally tailored variants of the ventilator, to increase the chances of it getting to actual patients.
To join our team as a volunteer or a partner, please reach out to us here: https://www.pubinv.org/polyventinventors/
Project Goals:
Our primary goal is to design a ventilator that:
- Meets patient safety standards in terms of monitoring, durability and resilience.
- Provides appropriate levels of clinical control to maximize therapeutic value and minimise risks to patients.
- Is easy to use and intuitive for experienced users as well as non-experts (thus freeing up expert clinicians for more demanding tasks), but also offers the ability to control advanced parameters to maximize patient benefit.
- Enables integration of a wide range of widely-available parts, components, materials and their manufacturing methods. For example, 3D printed or machined parts wherever possible to enable small-scale production, avoid supply chain bottlenecks, IP and licensing issues, and leverage under-utilized industrial manufacturing capacity.
- Has a modular design to simplify manufacturing and maintenance, and permit modules to be locally improvised based on part availability while still interfacing with the rest of the machine.
- Is based on a fully digital model, such that the impacts of utilizing alternate parts can be modelled and compensated for in the operating software without compromising performance.
- Can be manufactured at large scales using injection moulding, stamping, casting, and other mass-production methodologies.
- Has a robust digital control system, with the potential for remote monitoring as well as cloud-based data aggregation for performance and maintenance analytics, as well as collecting anonymized clinical data to provide large-scale cross-sectional and longitudinal data on patient outcomes.
- Is entirely open-source (software and hardware), with designs freely available worldwide.
To ensure the design becomes a reality, our secondary objectives are:
- To build supporting systems for design implementation, validation and monitoring.
- To create a scalable worldwide community platform to identify shortages, support the creation and dissemination of ventilator-related R&D, and channel human and other resources. Such an international community will cut through the existing economic, social and political barriers and help innovators around the world to work together to address this problem effectively.
PolyVent ventilator specifications:
PolyVent is a robust mechanical ventilator design formula for an emergency production scenario, which provides needed functionality, flexibility and adaptability based on the regional production and supply chain capabilities. A central mathematical blueprint provides a known degree of flexibility within the functional limits of the design. Highly modifiable, the basic design includes two independently-controlled air-pumping bellows driven by linear actuators. The system includes a multi-functional Venturi-based pressure/flow/volume sensor, an air-mixing and filtering system, an O2 concentrator integration possibility an electronics interface with optional GUI controls. Suitable for mass-production, PolyVent is a multi-modular concept, aiming to ease the pressure on the healthcare supply chain, and aid in the repair and replacement needs. Parts can be ordered from existing suppliers outside the healthcare chain, manufactured from a variety of materials and with a wide range of methods. The design aims to avoid IP issues and to allow unrestricted global access and implementation.
Designed for respiratory support modes: Synchronised intermittent mandatory ventilation (SIMV) Volume control ventilation (VCV) Continuous positive airway pressure (CPAP)
Where we are now:
After 6 months of design, review, and pre-prototyping of individual components, PolyVent has reached a stage where we need to bring it all together and build a full prototype to validate our designs in the real world. Working as a team spread out across multiple countries on three continents, the logistics of building a prototype were daunting until the Grand Garage in Linz, Austria stepped up and offered its
prototyping facilities for our use. Also supported by the City of Linz and the Sparkasse Oberösterreich, team members from Germany, the Netherlands, and Canada (supported by remote team members in India, Canada and elsewhere) mobilized to Linz for the Impact Innovation Weeks 2020 where aside from participating in panels and workshops, they will build a functional prototype of the PolyVent ventilator. Thus far, prototyping is proceeding rapidly, with 3D printing, CNC machining, programming, and electronics assembly ongoing for each of the modules of the ventilator. We are halfway through our two week programme and are on schedule to meet our goal of delivering a finished product. Along the way, we are capturing lessons learned (and learning them), and documenting our processes
and procedures for future use in refining designs, manufacturing, and meeting regulatory obligations.
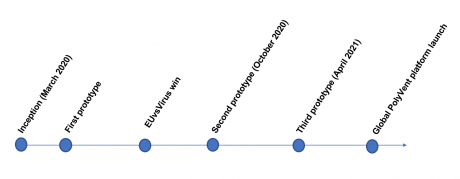
Current and Incoming Collaborations & Ventures
As one of the winners of the EUvsVirus Hackathon, we have now moved on to the matchmaking process. We have received a significant number of interests and offers from Institutional entities. We are in the process of solidifying our stance and direction of PolyVent prototyping, validation and production. We list here our ongoing progress with our partners:
- Public Invention, USA: Hosting the team and organisational support
- The Grand Garage, Linz, Austria: Discussions on hosting the European cluster of the project
- The City of Linz: Hosting the team, innovation week October 2020
- Engineers without Borders, NL: Hosting the team and organisational support
- Engineers Without Borders, USA: Discussions on partnership
- SIRIUS Global: Agreed to support the establishment of academic partnerships and other contacts
- Fonly LLC: Agreed to provide a unified electronics manufacturing blueprint for the control system
- Gitlab: Free gold membership for the team
What’s Next
After our weeks in Linz, our job is really just beginning. Having verified the viability our design, we need to keep pushing to ensure that our ventilator actually makes it to the people who need it. This means we need partners to support us in:
- Obtaining regulatory approvals in various jurisdictions
- Readying our designs for mass production
- Providing Cloud Computing facilities to support VentCloud
- Manufacturing support for initial runs of key components (e.g. circuit boards, bellows) to build the first production units
- Conducting initial patient trials in medical facilities
- Helping defray the costs of travel, communications, software and logistics